In today’s complex industrial landscape, optimizing operations while ensuring safety and compliance is paramount. Honeywell’s innovative Process Digital Twin solution offers a cutting-edge approach to achieve these critical goals.
“The answer is Honeywell Process Digital Twin,” stated a Honeywell Forge video recently, providing “a powerful and comprehensive solution for working with digital twins.”
The Process Digital Twin creates a virtual replica of your plant operations, allowing you to explore scenarios risk-free. As highlighted: “Using the technology allows your engineers to explore steady-state and dynamic scenarios in near real-time, monitor processes and assets, speed up diagnostics and set targets.” This capability empowers teams to identify and address potential issues proactively, avoiding costly downtime.
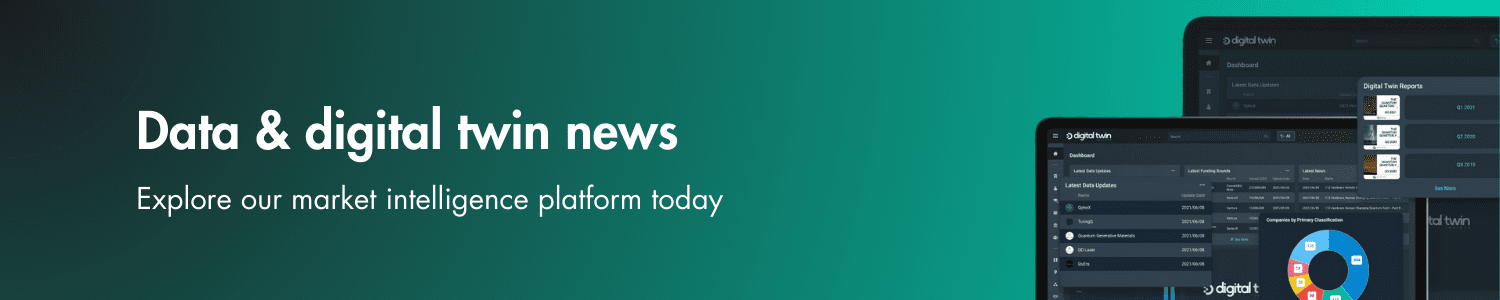
The Process Digital Twin facilitates seamless collaboration between operators and engineers. “Operators and engineers can also share data to collaborate and prioritize the squeakiest maintenance wheels to maximize ROI by fine-tuning the most critical areas of your network.” This shared visibility enhances decision-making and streamlines maintenance efforts, ultimately driving improved return on investment.
Sustainability is also a key consideration, and the Process Digital Twin excels in this area. The video stated: “Our pre-built process flows and predictive analytics help gauge exactly how much to amp up your production but keep on top of your emissions compliance.” By optimizing processes while adhering to emissions standards, companies can maximize value while minimizing their environmental impact.
In an era where agility, efficiency, and sustainability are paramount, Honeywell’s Process Digital Twin stands as a game-changer, empowering organizations to unleash their plant’s true potential while navigating industry complexities with confidence.
If you found this article to be informative, you can explore more current Digital Twin news here exclusives, interviews, and podcasts.