To remain ahead in the current manufacturing competition, industries are quickly moving on the path to fully exploit digital transformation. One of the concepts that developed to support this is the “digital twin,” which refers to the virtual replica of a physical product, process, or system enabling optimization and innovation using data.
Fujitsu is standing tall in leveraging this potential of digital twins. Recently, the company released a short film that underscores how it looks to solve some of the great challenges that manufacturers face nowadays: fragmented information flows, lack of traceability for change requests and silos of data in an organization.
These issues hinder quality control and impede companies’ ability to maintain consistent standards across globally dispersed production sites.
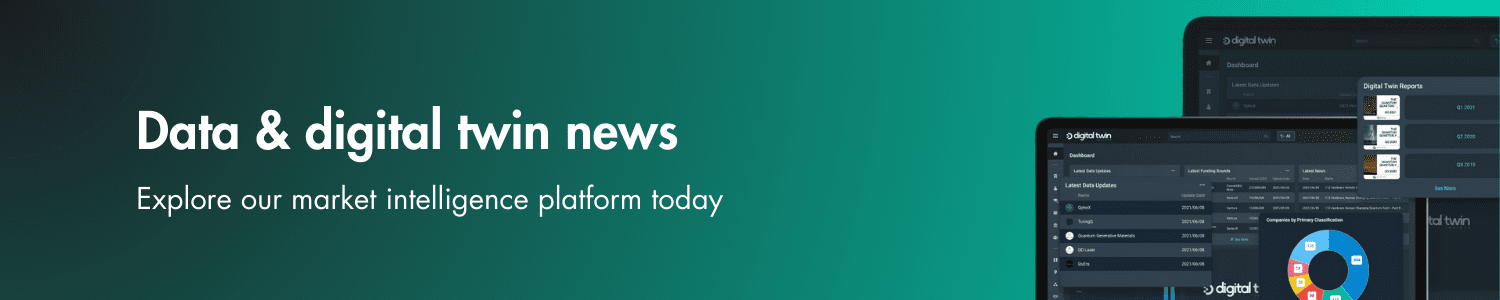
Fujitsu’s solution is its Manufacturing Operation Management suite, which fully digitalizes and connects the design, engineering, and production processes through centralized data integration. This allows for a true “digital thread” linking product design all the way through to manufacturing execution.
One core component is the digital representation of the Bill of Process. “Bill of process facilitates communication between design and manufacturing and accelerates standardization of manufacturing processes,” explains the video. By having a standardized, data-driven process model that all locations follow, companies can ensure repeatability and efficient multi-site production.
But Fujitsu goes beyond just process standardization. The digital twin allows for continuous process improvement by capturing quality data during manufacturing operations and feeding it back into design. “We support continuous quality improvement by providing continuous feedback on quality during the manufacturing process,” states the video. This closed-loop system transforms fragmented, localized quality control into an enterprise-level quality management capability.
Looking ahead, Fujitsu envisions further integrating digital twins with other Industry 4.0 technologies like AI, sensor networks, and immersive virtual reality environments. “Fujitsu will accompany our manufacturing customers to achieve your sustainable manufacturing goals with the vision of sustainable manufacturing growth,” the company says.
By putting digital twins to work to create a holistic, data-driven replica of the entire value chain of operations, manufacturers can break down organizational-function silos, harmonize processes, and realize better visibility and agility in their supply chain. Fujitsu’s digital thread approach connected by the digital twin underpins its mission to drive manufacturing innovation and enable “sustainable growth beyond” for its customers.
If you found this article to be informative, you can explore more current Digital Twin news here exclusives, interviews, and podcasts.